! Versión inglesa por el momento !
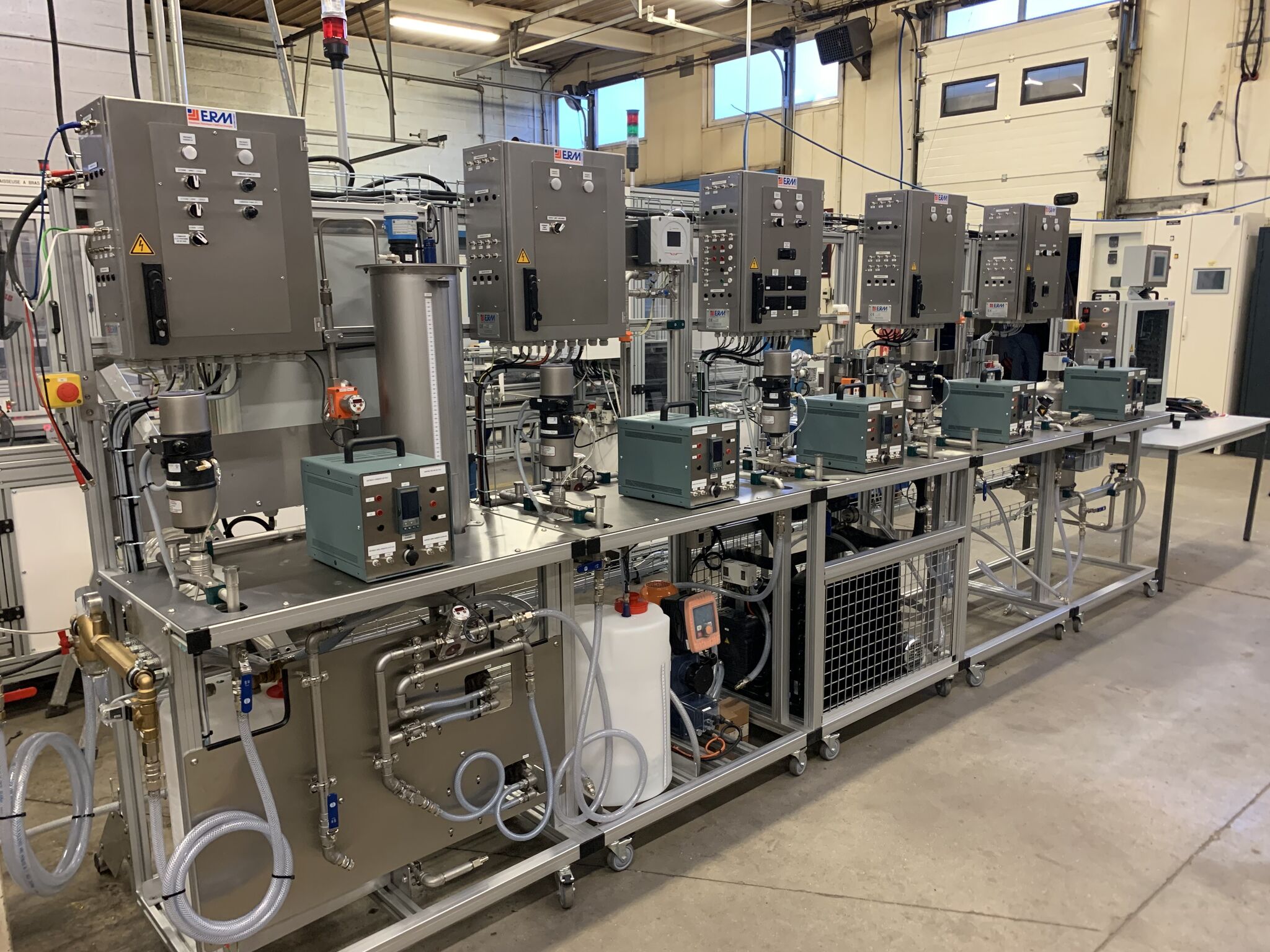
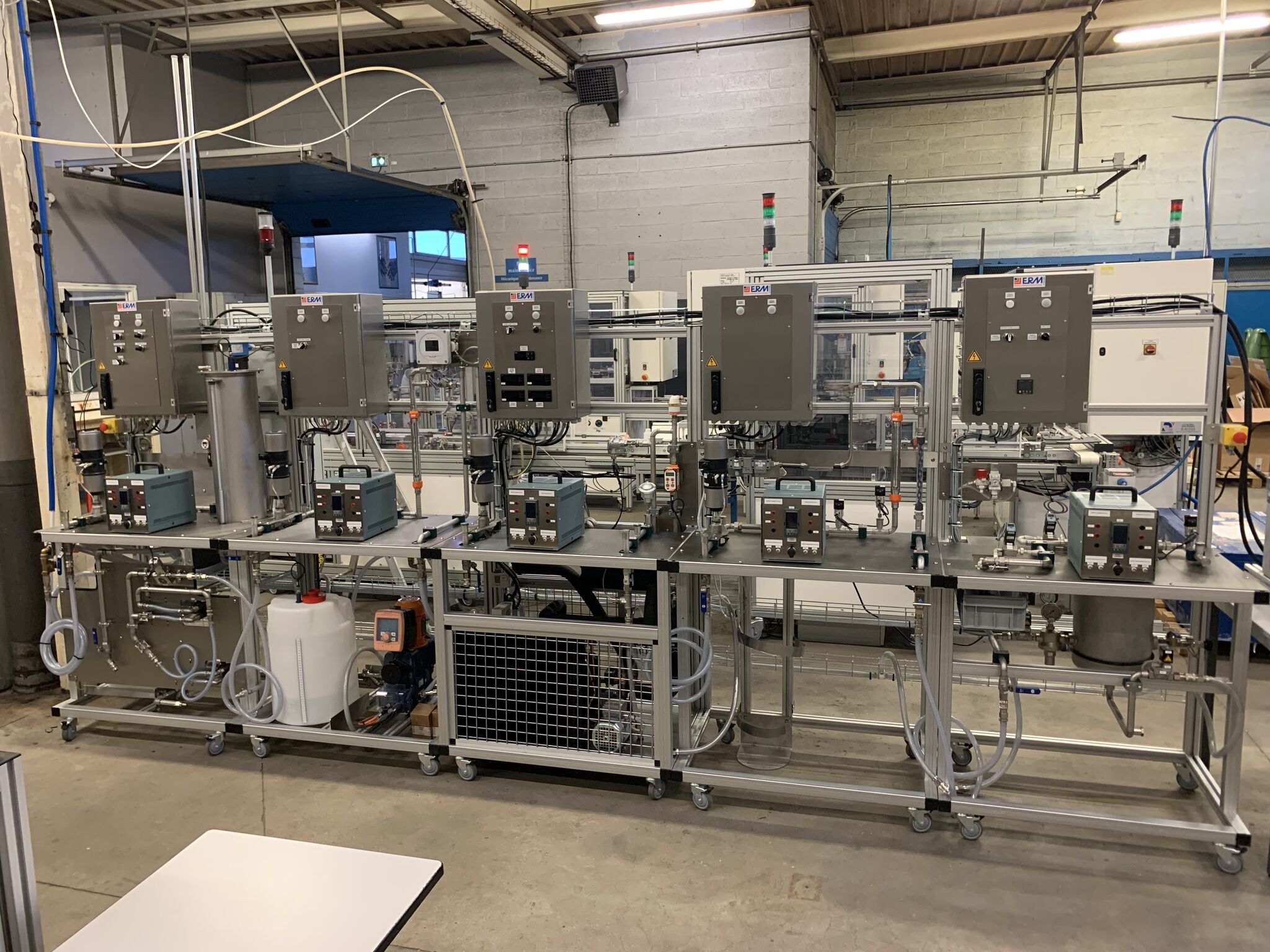
Modular didactic line for the production of carbonated drinks, to study process control
Project description
Teams from ERM Automatismes visited the AFPI in Dunkirk to install a Regulflex line. This educational production line is used to produce carbonated drinks for the study of regulation processes and associated instrumentation
Composition of the Regulflex line
The Regulflex line installed in Dunkirk comprises 5 operating units, 5 industrial controllers, a PLC module and an SNCC.
Each Regulflex line can contain the following systems:
- Buffer tank (Level:Flow): Level control (unpressurised storage), flow rate and instrumentation.
- Dosing (Flow Rate/Report): Liquid flow control (Dosing), ratio and instrumentation.
- In-line refrigeration (Flow/Temperature): Temperature control (Cooling), flow rate and instrumentation.
- Carbonation (Flow/Pressure): Gas flow control («CO2 Gas» carbonation), pressure and instrumentation.
- Pressurized storage (Pressure/Level): Pressure regulation (Storage under pressure), level and instrumentation.
- Industrial process controller: Industrial PID controller study module.
- PLC trainer for PID control: Module for studying PID control using PLC.
- Distributed Control System: Module for studying Digital Control Systems (DCS).
- Supervision: Process supervision via operator console.
- Calibration: Calibration equipment for sensors (current loop, pressure, temperature, etc.)
Little extras
This innovative concept for teaching process control, instrumentation and regulation is based on the use of a real process, in this case the production of soft drinks. This enables students to carry out practical work on the various parts of the manufacturing process in a fun way.
With the presence of a number of systems, the students learn about the main physical quantities (level, flow rate, pressure, temperature) as well as the easy implementation and contextualisation (water, air, and possibly colouring, syrup, CO2). They will also learn about simple (TOR, P, PI, PID, etc.) and complex (cascade, ratio, split range, etc.) control systems.
Modular systems allow each module to operate independently (stand-alone mode) or interconnected with the others (process mode).
Up to 12 students can work simultaneously.