ErmaLean
Didactic assembly line for learning Operational Excellence methodologies (Lean Six-Sigma)
Presentation
ErmaLean is an evolving workshop that confronts learners with realistic industrial situations, such as the assembly of a mechatronic assembly. This enables them to apply the continuous improvement tools and methodologies used in industry. The learning process alternates between production phases and periods of performance analysis, using Lean and Six Sigma tools. The adjustments made on the basis of these analyses enable the quality, cost and lead-time targets set by the customer to be achieved. To implement ErmaLean, you need a workshop space of at least 100 m², so that you can configure the different layouts required for your activities.
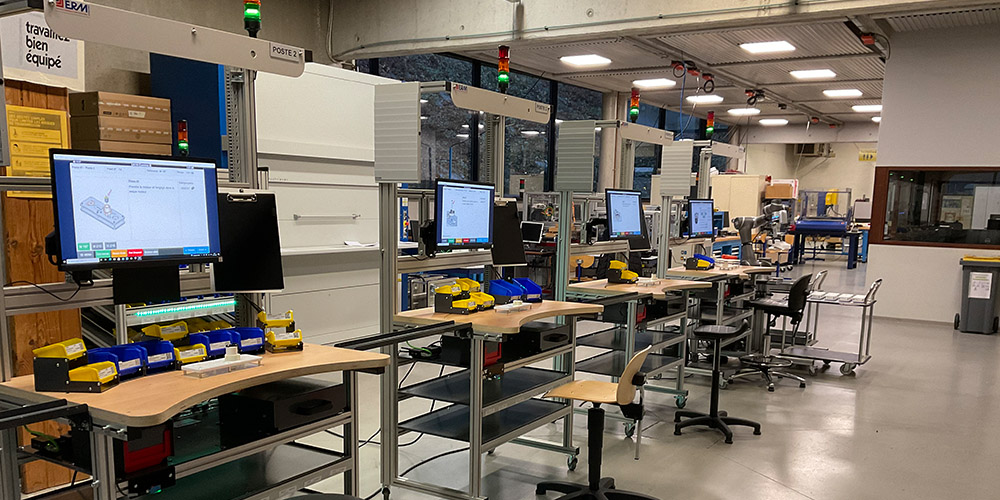
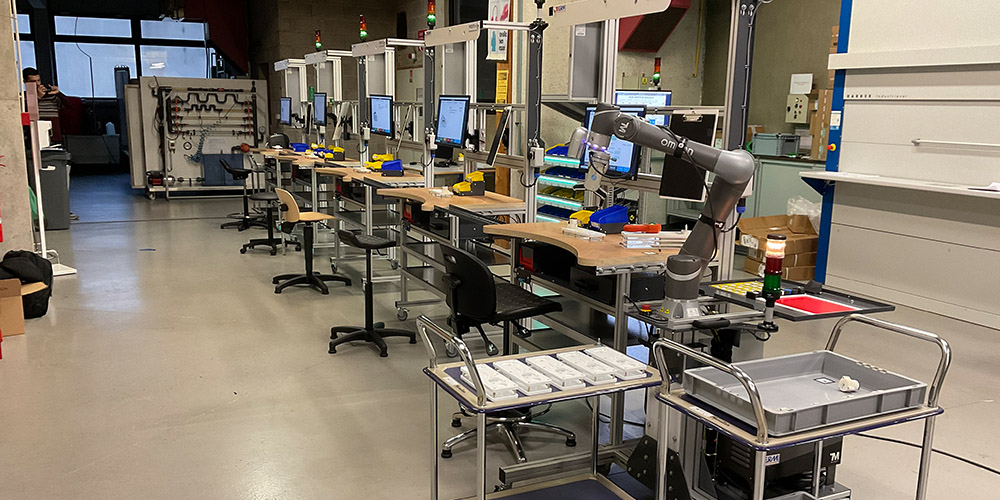
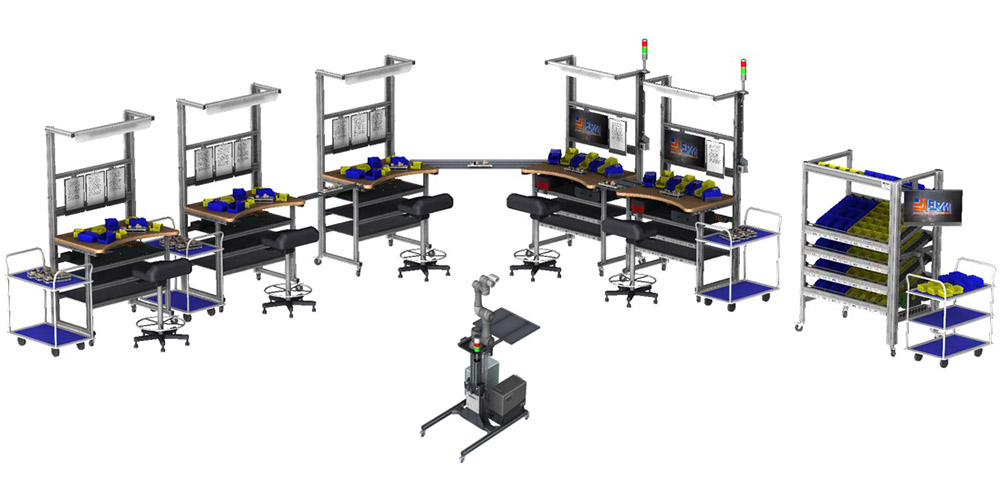
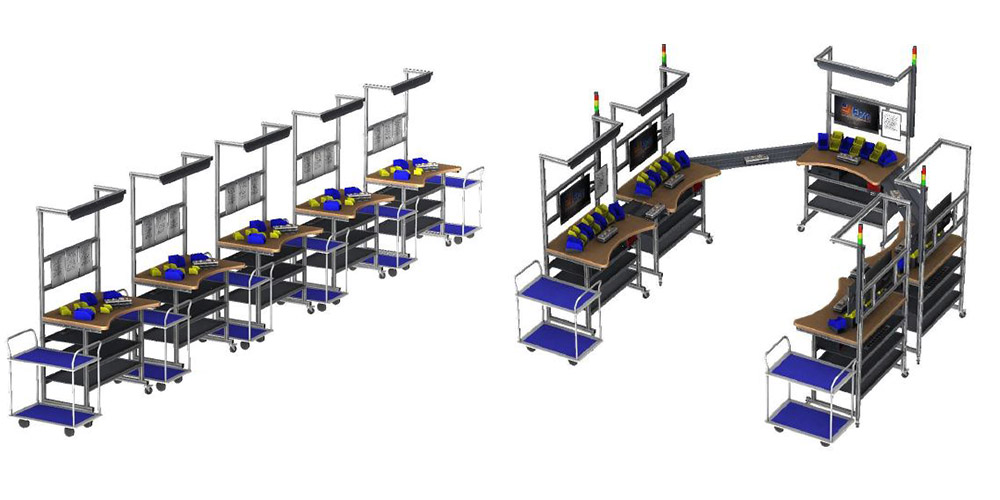
Key points
A management role
Including a supervisory PC with Wi-Fi connection, a whiteboard and communication media
Dynamic storage
Dynamic storage system designed to hold all the containers required for three product variants
Five assembly workstations
Modular, depending on the performance being tested, with scalable management and control elements. Allows several set-ups to be tested (independent, in-line, U-shaped). Provides RFID traceability on assembly pallets and transfers between workstations
Assembly tools
Integrated assembly tools and built-in control, some of which are connected to the supervision system (measurement of screwing torques, dimensions, conformity tests, etc.)
Handling equipment
Handling, component supply and inter-station transfers are designed for the WIP volumes of the various locations tested, with evolving performance levels for the entire process
Scalable
The evolution towards the assembly of other products is possible by the adaptation of the assembly trays and the modification of the documentations
Technical solutions
🔹Lean Manufacturing
🔸 Six-Sigma
🔹MES (Manufacturing Execution System)
🔸Digital procedures
🔹Connected tooling
🔸RFID traceability
🔹Industrial vision
🔸Mobile robotics
🔹Collaborative robotics
Our partners and suppliers
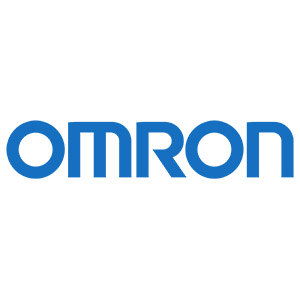
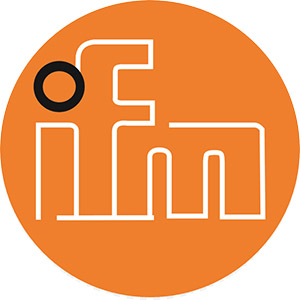
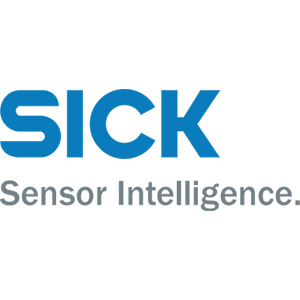
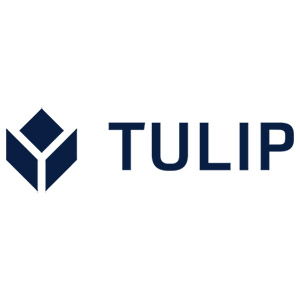
Teaching activities
• Practical application of the main tools used in Lean Six Sigma (VSM, Kanban, Capability, Variability...)
• Carrying out projects according to
the DMAIC process:
Implementing process improvement project
management tools and other teamwork tools
• Lead time:
Highlighting the impact of balancing the workstations’ workload
• Takt Time:
Measurement, analysis and
evolution of the flows of :
Material (batches, part to part), People (location) and Information
• Kaizen: Implementation of Kaizen tools (5S, TPM...)
• Quality: Implementation of Six Sigma tools (Capability; Regression; R&R; ...)
• Workshop management: Consideration of the different parameters of business management
• Ergonomics & Safety:
Impacts of ergonomic and working conditions in safety standards